自動化事例
カートン(段ボール)パレタイジングシステム
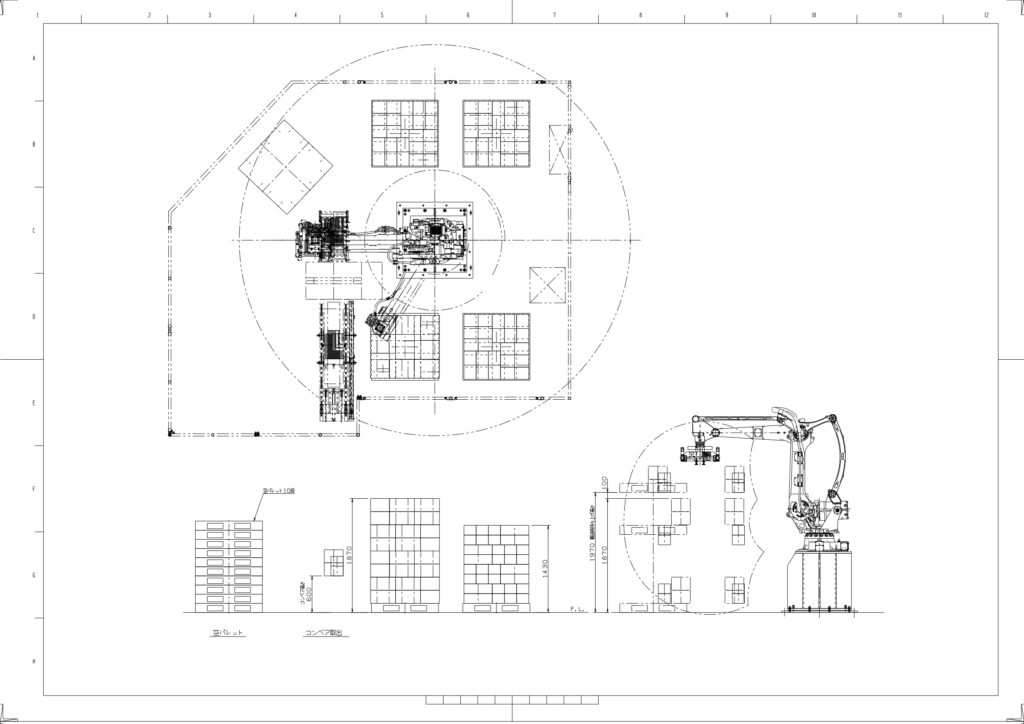
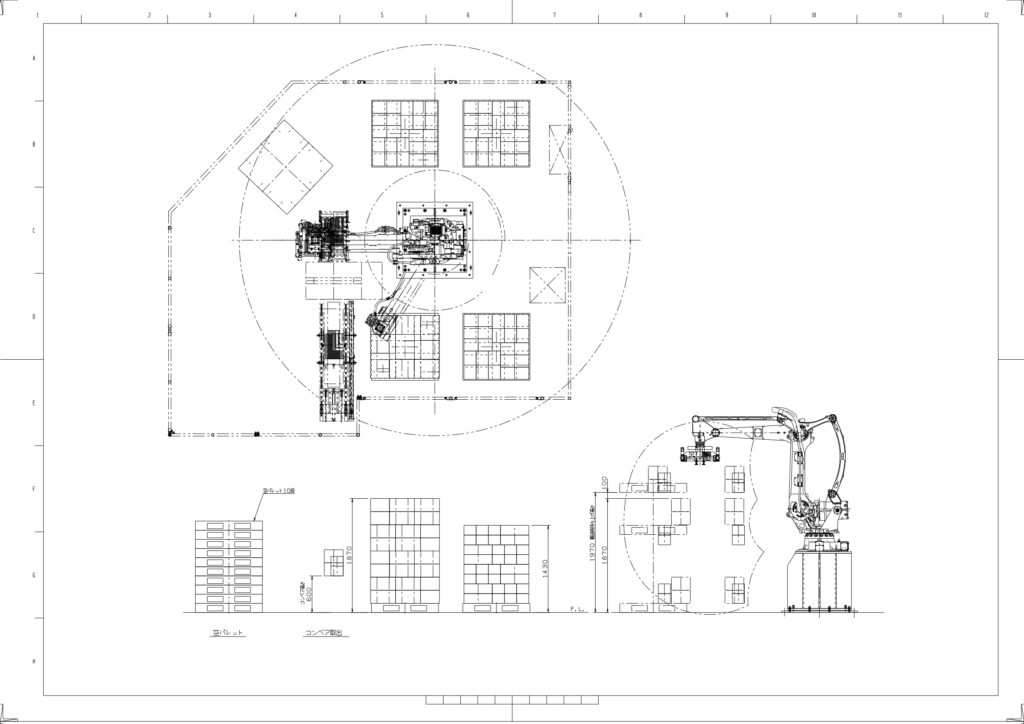
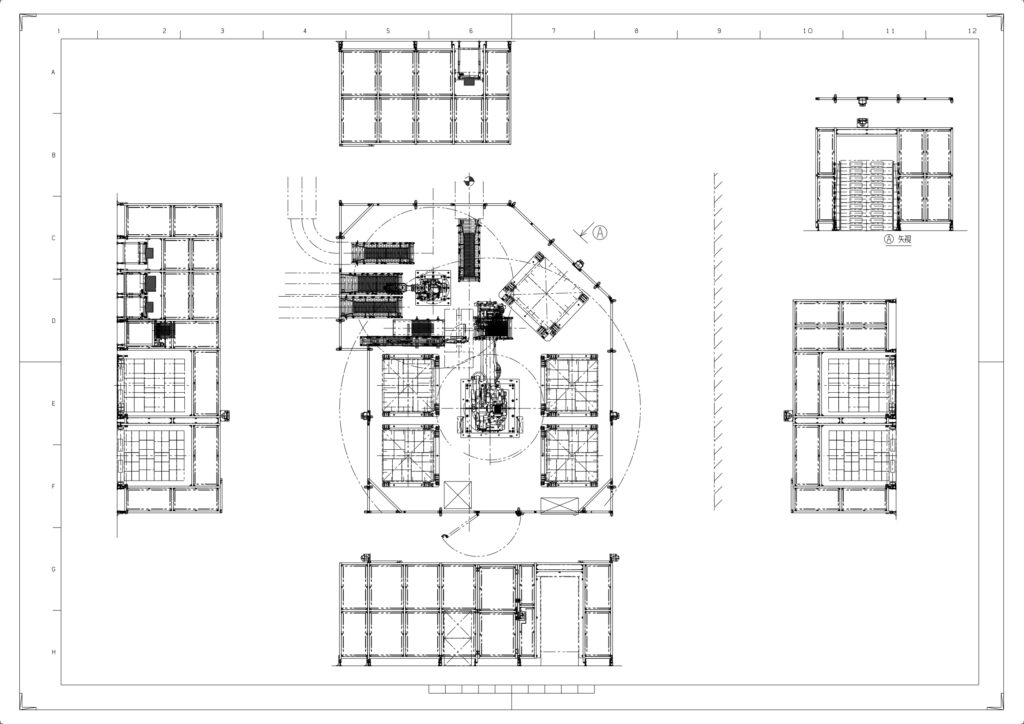
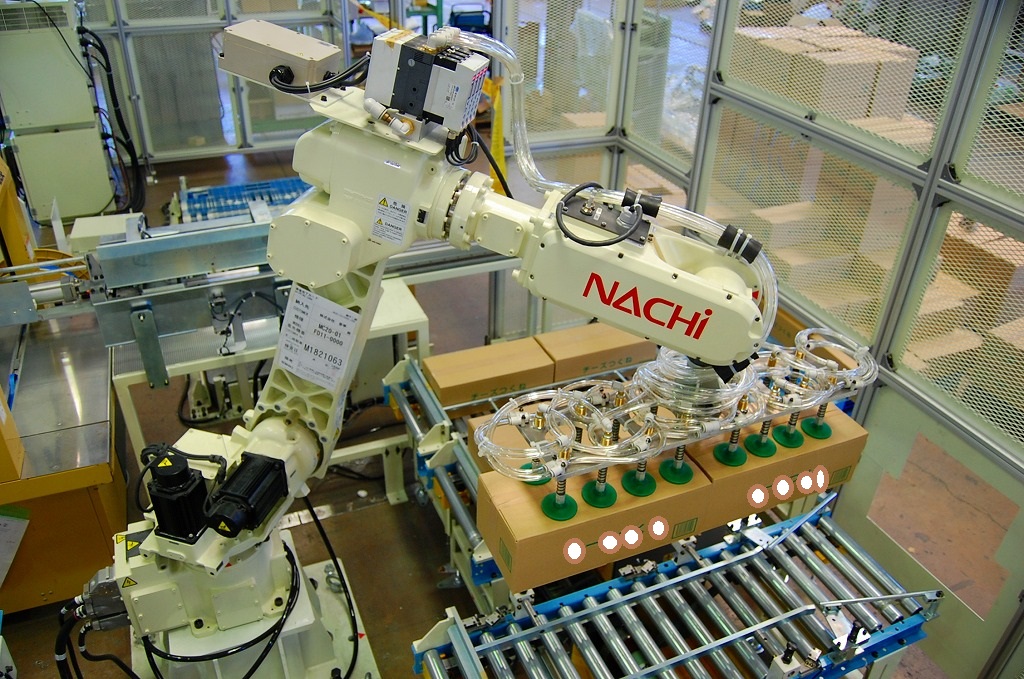
効果
労働生産性 | 3倍 |
---|---|
人数 | 6人⇒2人 |
労働時間 | 8時間(1人)x(2直) |
投資回収期間 | 3年 |
概算投資額 | 3000万円 |
概要
課題1 | 省人化したい |
---|---|
課題2 | 生産性をあげたい |
課題3 | 重作業をなくしたい |
用途 | 仕分け・梱包・包装 |
導入機器 | パレタイザー・デパレタイザー装置 |
対象ワーク | カートン(段ボール) |
業界 | 食品・食品機械 |
※こちらはあくまで概算・目安になります。
詳細につきましてはお問い合わせください。
導入前
これまでは、1日を通して3名×2交替制(2直)での対応が必要な作業体制でした。
前工程からは、7秒ごとに冷凍された食材入りのカートンが流れてきます。このカートンを上下2段に重ね、PPバンドで締めたうえで、決められたパターンに沿ってパレットへ積み込んでいく必要がありました。
積み終わったパレットはフォークリフトで出荷ヤードへ運ばれますが、この一連の工程には、
・積み込み作業とPPバンド掛け作業に常時2名
・フォークリフト専任で1名
合計3名の人員が各直に必要な運用となっていました。
導入後
効率化を目的に、ライン構成そのものを抜本的に見直しました。
まず、カートンを自動搬送可能とするため、ロボット1台が届く範囲に動線を確保。工場の壁を一部削除し、よりシンプルかつスムーズな物流フローを構築しました。
具体的な自動化のポイントは以下の通りです:
1.ロボットAによる自動積み付け
カートンを取り出し、そのまま上下2段での積み付けまでを一括で実行可能に。
2.自動バンド掛けの導入
市販のバンド掛け機に自動押し込み装置を追加することで、2段積みのカートンへのPPバンド締結を全自動で実施。
3.ロボットBの多機能ハンド化
ロボットハンドの工夫により、以下2つの作業を実現:
– 1m×1mパレットを最大10段まで積載・管理。積み込み前のパレットは4か所に設置可能で、パレット切替も停止なしで連続稼働可能。
– PPバンドで締結された2段積みカートンをバキュームで把持し、パターン認識に基づいて正確にパレットへ積載。
このように、ライン全体をロボット主導の設計に変更することで、前工程から流れてくるカートンを完全自動でパレットに積載可能となりました。
また、安全面にも配慮し、パレット搬出時に人が入っても自動ラインが停止しないよう、安全柵とエリアセンサーを設置しました。これにより、省人化と安全性の両立を実現しています