自動化事例
製品ブロッキング解消装置
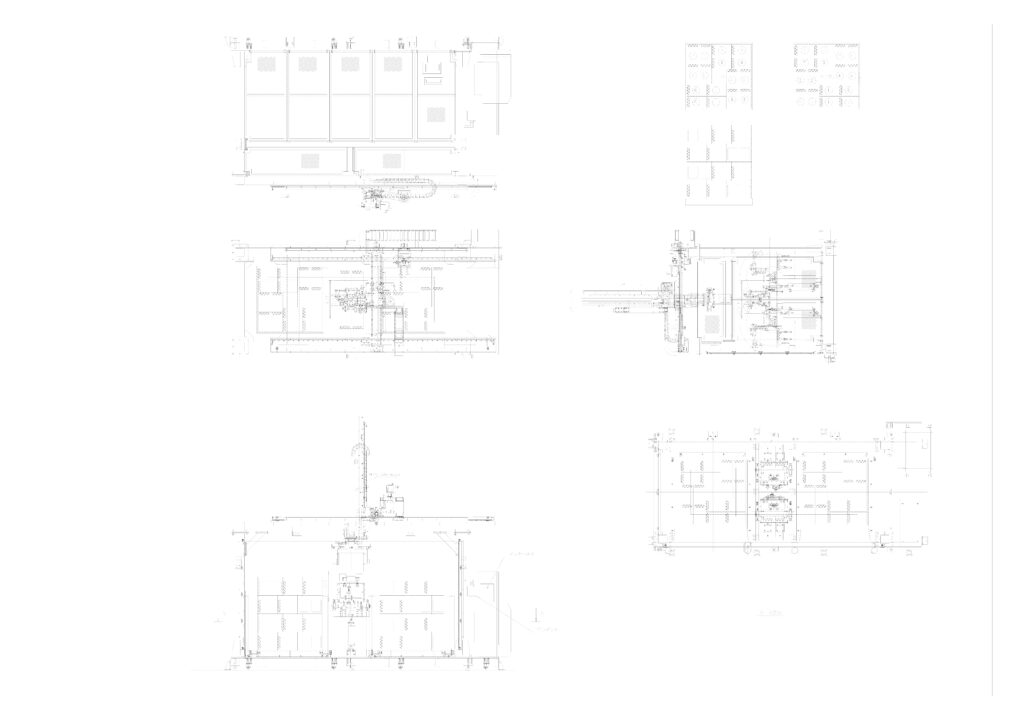
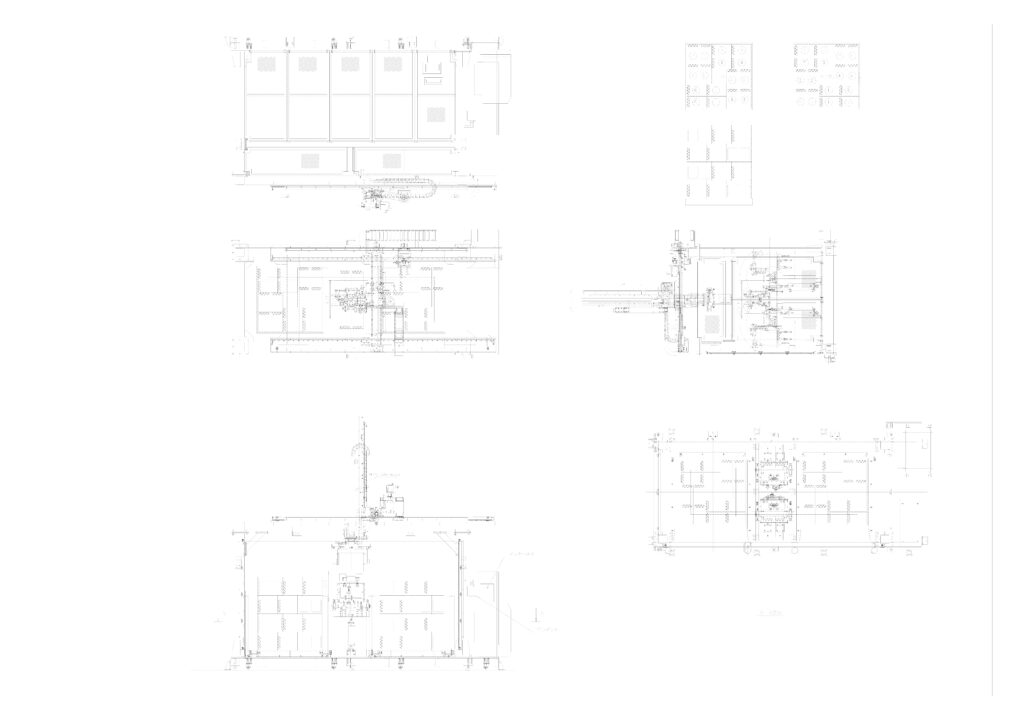
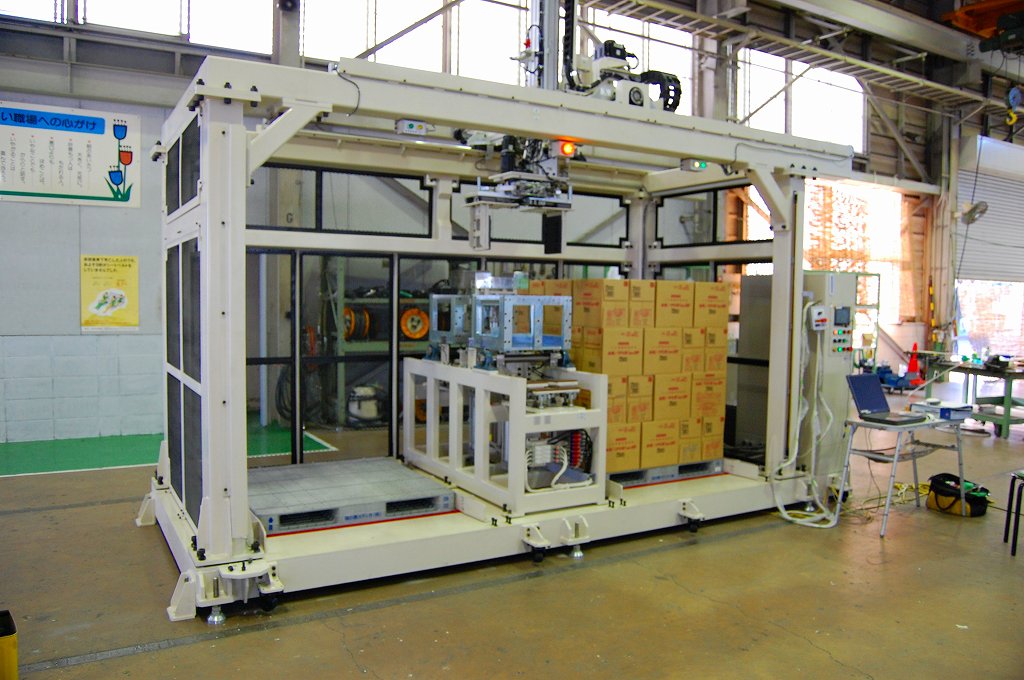
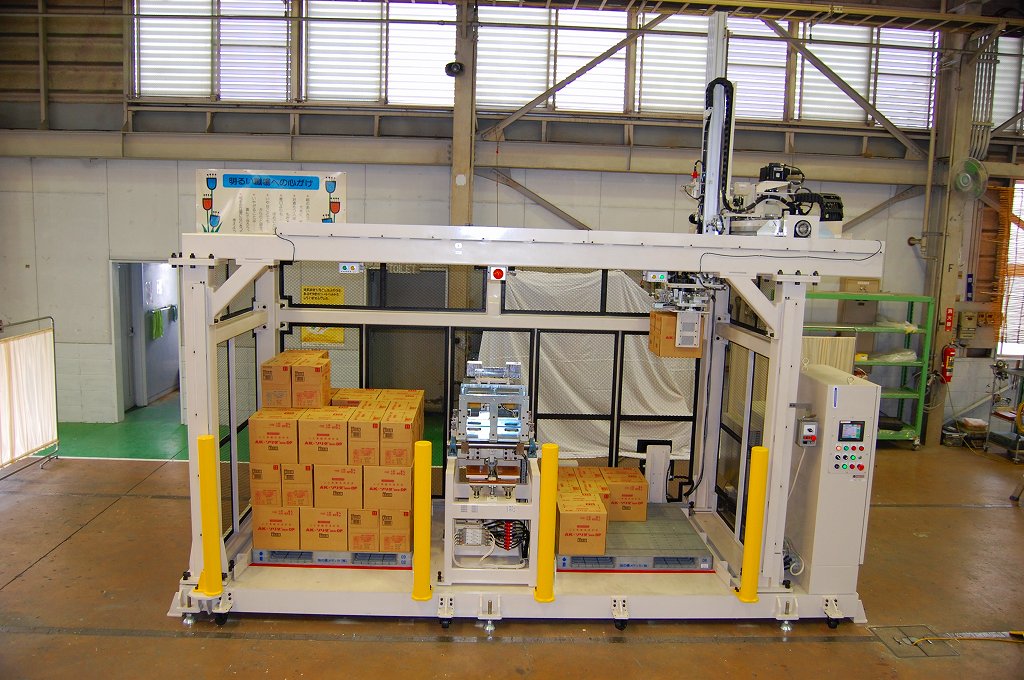
効果
労働生産性 | 3倍 |
---|---|
人数 | 1.5人⇒0.5人 |
労働時間 | 12時間⇒4時間 |
投資回収期間 | 4年 |
概算投資額 | 1,500万 |
概要
課題 | 省人化したい、不良品をゼロにしたい |
---|---|
用途 | 集積 |
導入機器 | パレタイザー・デパレタイザー装置 |
対象ワーク | カートン(段ボール) |
業界 | 医療・医薬機器 |
※こちらはあくまで概算・目安になります。
詳細につきましてはお問い合わせください。
導入前
ある商品をカートンに詰め、パレットに置いて、出荷前に、凝固するのを防ぐために、衝撃を与えて、詰み直し、パレットに積み上げてある製品(カートン)を1個ずつ取り出し、再度積み直しを行っていました。
その際、カートンの中身が凝固してしまう性質もので、見た目がよくない。そのため、凝固しないように手作業で、衝撃を与えながら、積み直しを行っていました。
衝撃を与えるという作業が余分に時間がかかってしまっていました。
中身のブロッキングを解消するために衝撃を与えてから再度積みなおしの作業を行っていました。
カートンの中身
製品が時間が経過すると固まる(ブロッキング)特性があるため、品質クレーム対応として作業をしていた。
導入後
パレタイザーと、凝固を防止する装置(シーソー型の衝撃装置)を導入しました。
これにより、手作業でカートンをパレットに積み上げた後は、ローダーで2個取り出し、ブロッキングを解消する装置(シーソー型の衝撃装置)に投入、複数回衝撃を与えたのちに再びローダーで受け取り隣のパレットへ積み上げる装置を納入したことで作業者はパレットの出し入れのみの作業となりました。
結果品質向上、労働時間短縮、労働環境向上につながりました。